|
Home
Index
Test machines
Test ancillaries
Measurement
Production
Services
Miscellaneous
|
|
|
Universal joint test rig
|
Application
The rig is designed to evaluate drawn cup bearings in steering column universal joints by
-
rotational endurance testing
-
bearing seal efficiency.
Principle of operation
The input to the test piece is driven under angle servo control (drive motor) with the test piece output under torque servo control (brake motor).
|
Description
-
A flat-topped table mounting 2 electric servo motors and an environmental chamber surrounding the parts under test.
-
Recirculating water-salt-sand spray generation system (mounted under the table).
-
Electrical cabinet housing 2 vector drives, main rig isolator, fusing and 24 volts control relays (mounted under the table).
-
Control cabinet with computer and printer.
Table
-
22mm ground steel top 1.8m x 0.8m, 0.9m high, with height-adjustable anti-vibration mounts.
Control cabinet
-
600mm x 600mm x 2 metre, 19inch cabinet housing RISC PC (233 megahertz RISC processor, 1.2gb hard disc) and interface cards, electronic control rack and drives control panel.
-
Colour inkjet printer for hard copies.
|
Performance specification
The input drive motor and the output braking motor gearbox pair are identical 4 pole 5.5kW motors fitted with rightangle gearboxes giving:
-
Maximum torque capability of ±100 Nm
-
Maximum frequency 0.8 hertz for a rotation ± 720° from 0° (total 2880°).
Operating software
The programs, written by Si-Plan, enable test sequences to be specified, saved and recalled. Angle, torque, spray, temperature and logging requirements can all be set, offering a versatile control package.
There is a dynamic data display on screen and capture of test results to disc.
Program options include:
-
Rotational endurance.
-
Fatigue Testing.
-
Backlash testing (with optional LVDTs).
|
Motors
-
The two motors are controlled through Eurotherm 620 Vector drives. These Vector drives are 4-quadrant controllers allowing the power generated in the braking motor to be regenerated onto a common DC bus and circulated back to the input motor, therefore requiring only system losses to be drawn from the mains supply. This has the benefit of significant energy cost savings and minimises heat generation within the test laboratory.
-
The rig is capable of testing either one or two universal joint/shaft units mounted horizontally at resolved angles of 0° up to 40° maximum.
-
The driving and braking motors lie on parallel centre lines, as illustrated below.
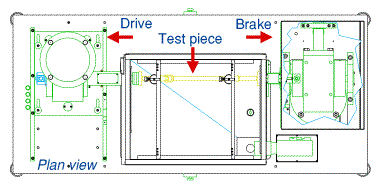
-
The drive motor moves horizontally in an axis perpendicular to the parallel centre line of the two motors.
-
The position of the braking motor is fixed. This arrangement enables the different lengths of customer components and installed angles to be accommodated. The output shafts of the drive and brake motors are fitted with bosses providing four M8 tapped holes on a 44.45mm pcd and a counterbore to maintain concentricity of component-specific adaptors (component adaptors are not included as standard).
|
Environmental Facility
-
Insulated stainless steel enclosure with removable lid.
-
The shaft from the fixed braking motor passes through the wall of the stainless steel tank with a lip seal to protect the braking motor and torque instrumentation from heat and water/salt/sand spray.
-
The shaft from the movable driving motor passes through a slot in the side of the stainless steel tank with provision to close off the unused areas of the slot.
-
One nozzle for each universal joint directs the water/salt/sand spray. The water/particle solution drains to a reservoir and recirculating pump situated under the table (see over).
-
Heat is generated by a hot-air heat source mounted locally to the environmental chamber without recirculation, operating at temperatures from ambient up to 200°C.
-
Water/salt/sand spray is delivered at ambient temperature.
Services
-
The rig is supplied ready to connect to a 415 volt AC 3 phase isolator, rated at 30 amps.
|
Interfaces
-
There are 2 spare analogue input channels for the connection of external instrumentation.
-
There are 2 spare analogue input channels for the connection of optional backlash (radial clearance) measurement equipment
Documentation
-
Documentation is provided in English.
|
Special requirements
Si-Plan Electronics Research Ltd has a history of building special rigs to customer requirements. The company is able to carry over this service to its standard product range, giving a flexibility to meet the needs of each customer - and in-house CAD systems and CNC machining mean a realistic delivery time will be achieved.
|
Updated 20 April 2005
|