
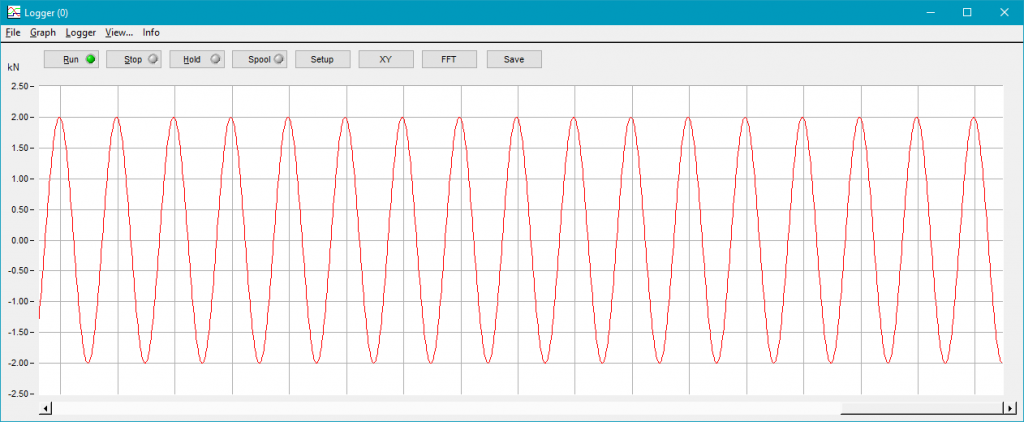
Vibrophore® Resonant Machine Control & Data Acquisition
Features
- Free-standing PC as user interface
- Remote pendant for crosshead adjustment
- Electronics cabinet housing
- Twin 400W power amplifier
- Digital servo-controller
- Crosshead motor amplifier
- DC Power unit
- Transducer signal conditioning
The computer interface window replicates the options for setting parameters available on Si-Plan’s solid state control and measurement electronics.
- Cycles counter Set cycles limit; display of cycles done and cycles remaining
- Crosshead Set mean load. Select auto or manual control. Select manual movement up or down
- Dynamic control Set dynamic demand. Select Run or Stop test
- Dropdown menu Select predefined running parameters
- Load cell Connected loadcell display
- DPMs display figures indicating the state of the test: Frequency, Mean, Compression; Range; Tension
Where required, customer specific software and user interface can be offered.
- Data logging for every cycle and/or every nth cycle and/or every 2n cycles to to screen and/or a CSV file which can be imported into spreadsheet programmes.
- Confugurable data fields include Mean, Range, Peak tensile load and Peak compressive load and cycles.
Further background information
Since the early 1970s Si-Plan has manufactured replacement controllers for Vibrophore Resonant Test Machines. The first systems replaced the original valve-based controllers supplied with the Vibrophores. They provided solid state analogue control, bringing better control of test loads and much improved reliability and ease of use. Many of the early Si-Plan Vibrophore controllers are still in daily operation.
The analogue controller was continually developed until 2004, when it was superseded by the digital controller, with computer user interface and data logger.
Resonant machines come in a number of forms and common names are Si-Plan®, Amsler®, RUMUL®, Zwick®, and Instron®.
Resonant test machines are ideal where a large number of cycles is required, with typical test frequencies in the range 80-300Hz.
Resonant machines are very energy efficient with power requirements on a test of 10kN-100kN at 120Hz, for example, in the order of 600 watts. Contrast this with a servo hydraulic machine which would test at around 30Hz and require in excess of 20kW.
The main application is HCF (high cycle fatigue) in the following areas
- materials testing – research into material properties
- bolt and fastener testing – often in the aerospace industry
- reinforcing bar testing – in the steel/construction industry
- pre cracking fracture toughness specimens